A year ago, Eramet Ideas, the Eramet Group’s research and development center, welcomed the SEM (scanning electron microscope). A world first, this equipment enables us to observe ores and metals down to a scale of several tens of nanometers, in order to create chemical maps. “This tool enables us to better understand the distribution of chemical elements within minerals and metals,” explains Mickaël Dadé, Metallurgy Research Engineer at Eramet Ideas. “The knowledge made possible by such a tool is a considerable asset for Eramet’s entire value chain, in many fields.”
Understanding minerals for better mining
Using SEM, samples taken in the field by Eramet’s Exploration unit are analyzed to identify the minerals of interest present, understand the geological processes leading to enrichment in strategic metals and thus estimate the economic potential of the area studied. It is thanks to this preliminary stage that the Group can imagine future mines and the best way to develop the resource.

EDS (energy dispersive spectroscopy) mapping of a manganese oxide-rich sample from a deposit at Buritirama, Brazil
Improving mining and metallurgical productivity
Microscopic observation of ore samples provides a detailed understanding of the texture of the minerals of interest, so that the best impurity removal strategy can be adopted. For example, observing alloys with SEM precision enables us to study the impact of a new casting process on the microstructure of silico-manganese.
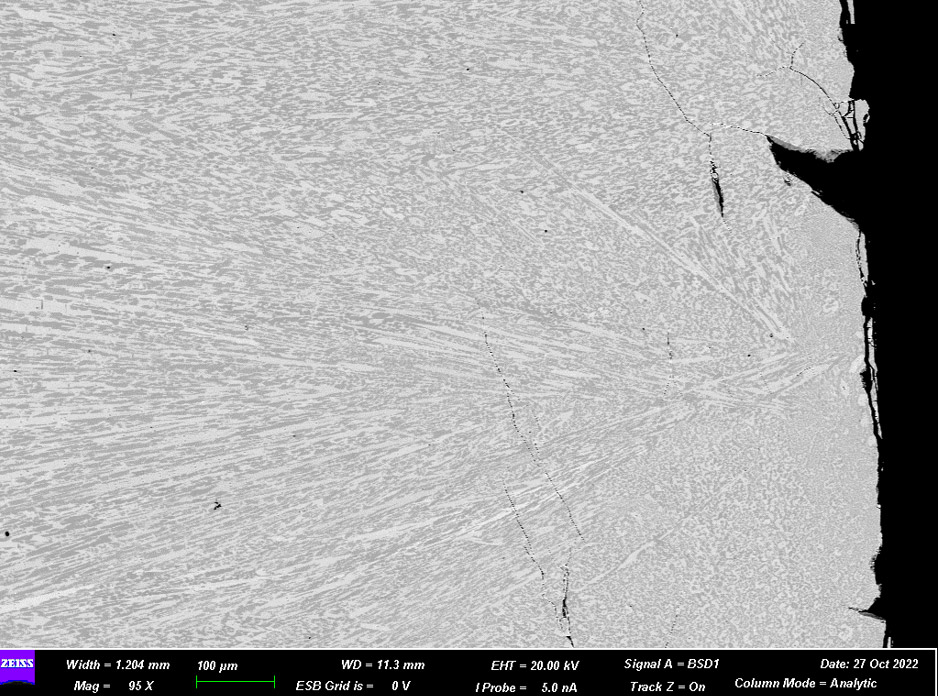
SEM microstructure of a silico-manganese alloy after innovative casting
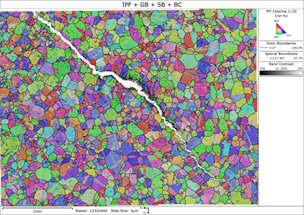
Illustration of intergranular failure of the CMM shell after several mechanical stresses
In addition to optimizing enrichment and smelting processes, SEM is also used to identify potential mechanical and metallurgical failures on critical parts that could lead to breakage or production stoppage. This was the case this year on a furnace shell at the Moanda metallurgical complex (CMM), and more recently on the GCO pump.
In the service of safety
The microscope also contributes to the safety of operations: this was recently verified on samples from the Exploration department, containing a fibrous phase of unknown nature. Before being crushed, this sample was passed under the SEM column, coupled with a RAMAN spectrometer, revealing that it was in fact marialite (from the Feldspar family and therefore of no particular risk) and not asbestos, a mineral which is extremely toxic if inhaled.
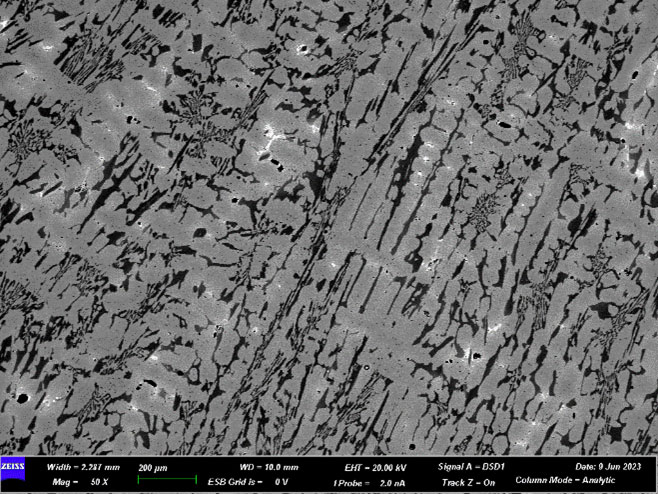
Microstructure of a pig iron used for critical components of the GCO pump
What does the future hold for MEB?
“We’re now in a position to observe and understand in a way that wasn’t possible before. The SEM represents a tremendous technological advance, enabling us to gain a higher level of knowledge of our ores and metals”, says Mickaël Dadé, research engineer in metallurgy. “The future development of this tool will be the geometallurgical application itself: in other words, the acquisition of knowledge that will form the basis for improving knowledge of the Group’s deposits, as well as the treatment of ores in extractive metallurgy processes.”